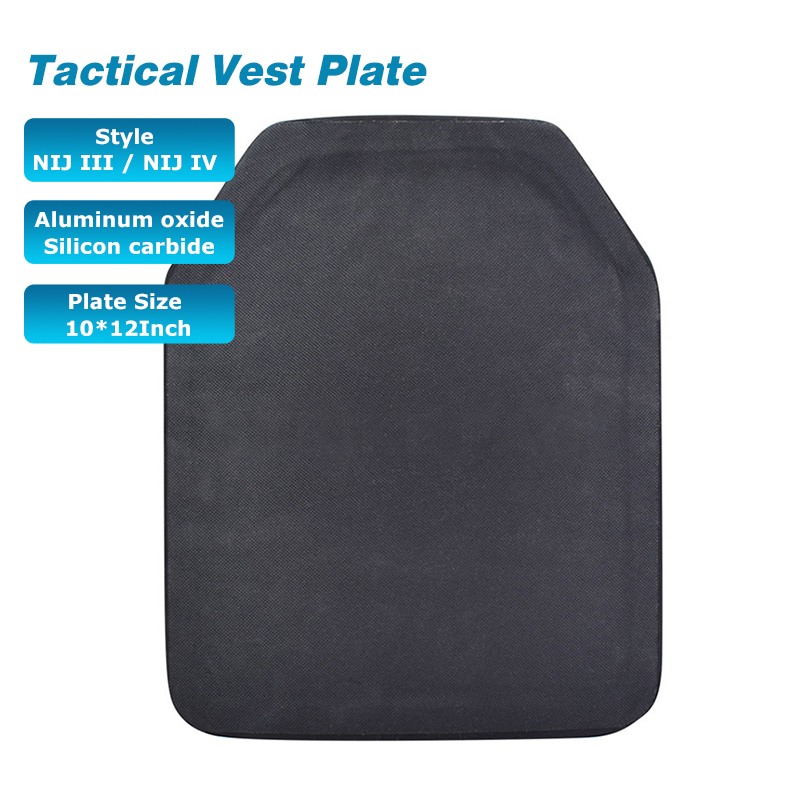
Aluminum oxide (Al₂O₃) and silicon carbide (SiC) are both ceramic materials used in bulletproof panels, but they have distinct properties that affect their performance in ballistic protection:
Material Composition and Performance:
-
Aluminum Oxide (Al₂O₃):
-
Composition: Made from aluminum oxide, which is a type of ceramic material.
-
Performance: Aluminum oxide panels are generally less hard and less dense than silicon carbide panels. They provide good protection but are not as effective against high-velocity rifle rounds as silicon carbide. Aluminum oxide is often cheaper, making it more accessible for budgets where cost is a significant factor.
-
-
Silicon Carbide (SiC):
-
Composition: Silicon carbide panels are made from silicon carbide, known for its high hardness and strength.
-
Performance: SiC panels offer superior protection against higher-velocity rifle rounds and armor-piercing bullets due to their greater hardness. They are more effective at stopping bullets by shattering or deforming them upon impact, which disperses the bullet's energy more efficiently.
-

Bulletproof Ratings and Protection:
-
Ratings Overview:
-
Bulletproof panels are rated according to standards like those set by the National Institute of Justice (NIJ). These ratings indicate the level of ballistic protection provided:
-
Level II: Designed to stop common handgun rounds like 9mm and .357 Magnum.
-
Level IIIA: Protects against most handgun rounds, including .44 Magnum.
-
Level III: Can stop rifle rounds like 7.62mm NATO (M80 ball).
-
Level IV: The highest level, capable of stopping armor-piercing rounds like .30-06 M2AP.
-
-
-
Specific Protection by Material:
-
Aluminum Oxide Panels:
-
Typically used for lower to mid-tier ballistic protection. They are often found in Level II and IIIA armor, providing adequate protection against handgun rounds but may struggle with high-velocity rifle ammunition. They might not be as effective for Level IV protection without additional composite backing materials.
-
-
Silicon Carbide Panels:
-
More commonly used for higher levels of protection due to their superior hardness. They are often part of Level III and IV armor systems. Silicon carbide can effectively stop both high-velocity rifle rounds and armor-piercing bullets, making them suitable for environments where threats include military-grade or armor-piercing ammunition. For instance, a Level IV plate made from silicon carbide can protect against .30-06 M2AP and similar rounds.
-
-
Bullet Sizes and Ratings:
-
Level II: Protects against:
-
9mm FMJ RN at 1245 ft/s
-
.357 Magnum JSP at 1430 ft/s
-
-
Level IIIA: Protects against:
-
.357 SIG FMJ at 1470 ft/s
-
.44 Magnum SJHP at 1430 ft/s
-
-
Level III: Protects against:
-
7.62mm NATO (M80 ball) at 2780 ft/s
-
-
Level IV: Protects against:
-
.30-06 M2AP at 2880 ft/s
-
When choosing between these materials, considerations include the specific threat level anticipated, budget constraints, weight tolerance, and the desired level of protection. Silicon carbide generally provides a higher level of protection at a lighter weight but at a higher cost, while aluminum oxide offers a balance of cost and effectiveness for less severe threats. Remember, the effectiveness of these panels can also depend on the design of the armor system, including the backing material used in conjunction with the ceramic plates.